Panoval Label S.A. è stata originariamente fondata nel 1991, in Svizzera. Basandosi sui punti di forza dell’azienda in Estremo Oriente, nel 2017 è stata fondata Panoval (Asia) a Ho Chi Minh City, Vietnam. Questa struttura all’avanguardia costruita appositamente comprende più linee di rivestimento e una camera bianca certificata ISO Classe 6 per prodotti di fascia alta che richiedono la più recente tecnologia di rivestimento. L’azienda è inoltre certificata ISO 14644-2.
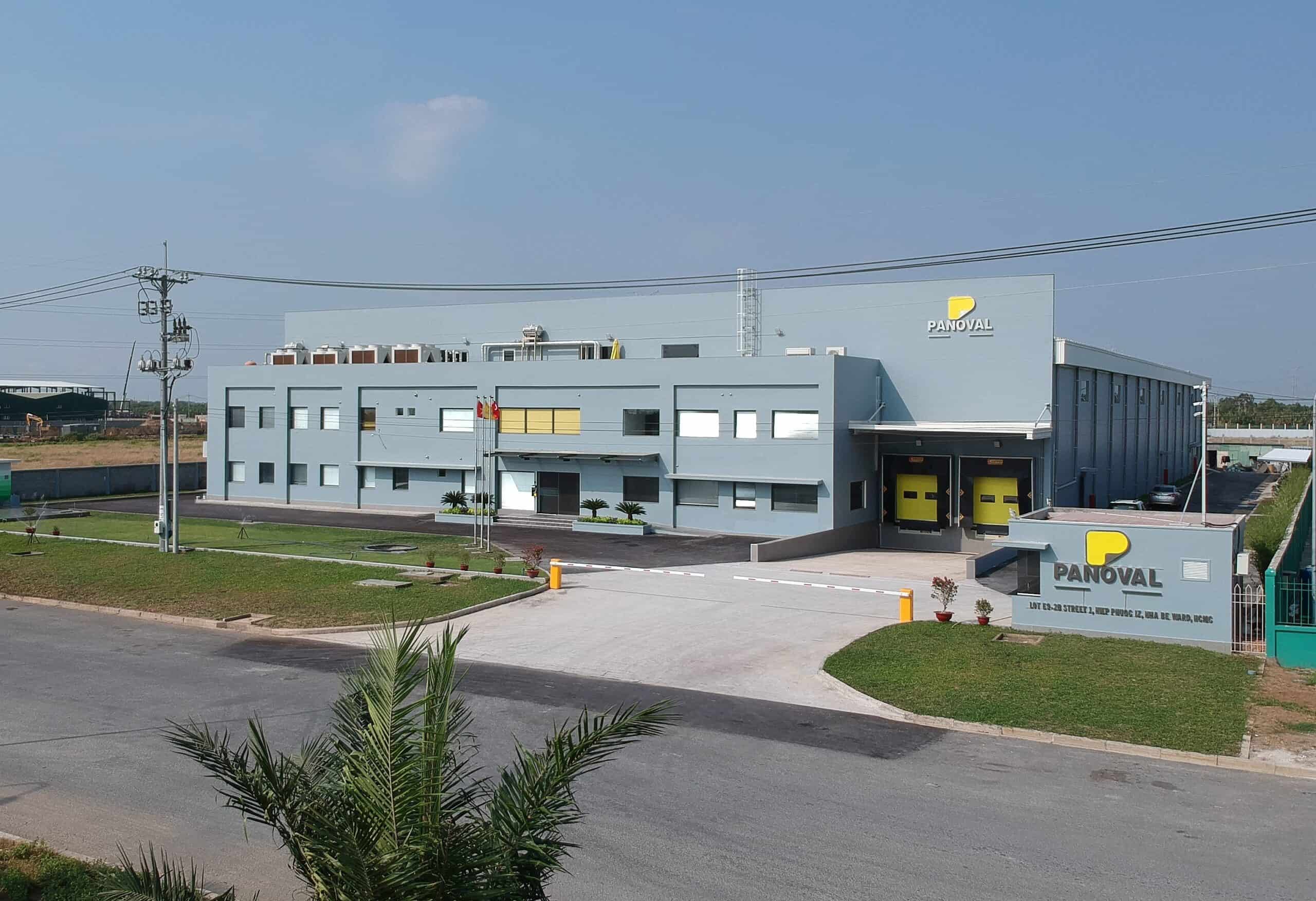
Oltre il 60% del volume globale di etichette autoadesive viene prodotto in Estremo Oriente, comprese quelle per applicazioni elettroniche, mediche e farmaceutiche. Questo è il motivo principale per cui l’azienda è stata fondata in Vietnam, anche se la proprietà complessiva rimane europea. Nonostante abbia un solo sito di produzione, Panoval lavora a livello internazionale con rivenditori e clienti diretti e ha costruito un business con presenza globale. La loro agilità produttiva e la reputazione di flessibilità li hanno portati a diventare un fornitore leader di etichette specializzate e non standard. I clienti tipici sono rivenditori di imballaggi flessibili, trasformatori di etichette e stampatori convenzionali.
Panoval impiega attualmente 25 persone ed è in continua espansione. Il team di gestione è composto da professionisti esperti e operativi a livello internazionale con una vasta esperienza nello sviluppo e nella produzione di laminati per etichette per le applicazioni più esigenti. Il direttore Wilco van Zwieten è entrato in Panoval come direttore delle vendite nel 1993 e ora è una parte fondamentale di quel team. Il suo compito è promuovere nuove attività e ritiene che il progresso tecnologico e l’innovazione siano fondamentali per il loro successo. Come spiega: “In un mercato così competitivo, sono le dimensioni relativamente piccole dell’azienda e la gestione di due linee di rivestimento molto diverse che ci permettono di avere così tanto successo. Oltre al lavoro tradizionale di volume più elevato che svolgiamo, il nostro team di produzione è in grado di eseguire una moltitudine di lavori specialistici più piccoli, a volte cambiando prodotto tre o quattro volte in un turno. Utilizziamo la più recente tecnologia hot melt UV per supportare i nostri sistemi a base di gomma. Questa tecnologia UV è l’unica che può potenzialmente sostituire i rivestimenti a base solvente… non subito, ma tra dieci o quindici anni. Per fare ciò, è necessario disporre di una soluzione di polimerizzazione UV di alta gamma con tutti i fronzoli che supportano tale tecnologia. E questo è ciò che abbiamo progettato, in collaborazione con i produttori di macchine e GEW, in modo da poter soddisfare tutte le nostre esigenze nei prossimi cinque-dieci anni. Siamo a prova di futuro.”
Progettato e prodotto nel Regno Unito da GEW, il sistema di essiccazione UV personalizzato di Panoval comprende cinque gruppi lampada NUVA2, con la capacità di ospitare fino a sette gruppi lampada in tutto, montati su un rullo raffreddato da Ø1000 mm su una linea di rivestimento Sung An Machinery (SAM). Le lampade sono montate attorno al tamburo su un solido gruppo telaio, che è separato dal gruppo rulli e scorre via dalla sua posizione impegnata su binari. Ciò consente l’accesso alla superficie del rullo e alla parte inferiore del gruppo lampada.
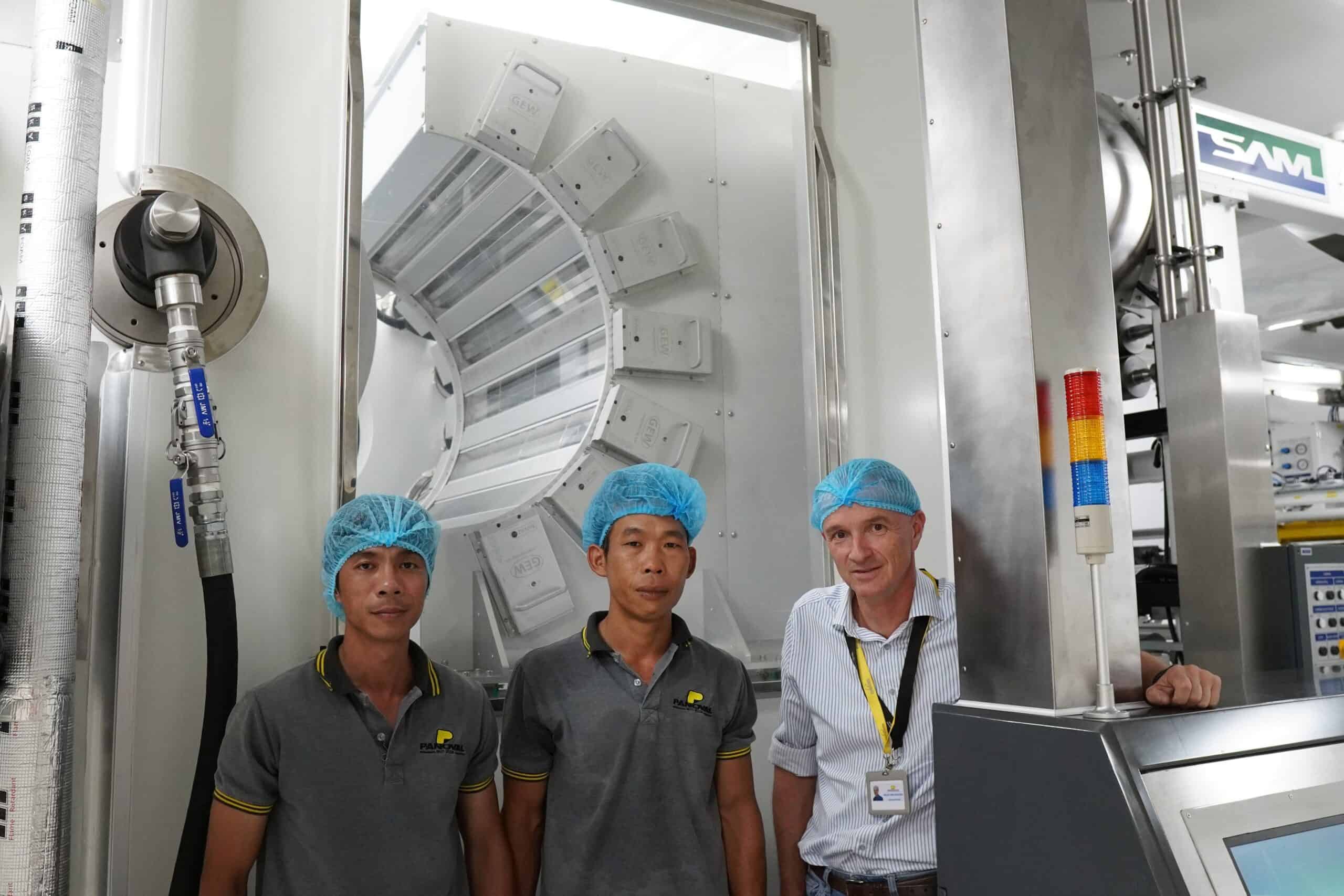
Inizialmente alla ricerca di una soluzione di essiccazione UV, van Zwieten è stato indirizzato a GEW da un socio malese che aveva recentemente collaborato con GEW per la progettazione e l’installazione di un sistema di essiccazione UV per applicazioni di rivestimento distaccante. Van Zwieten ricorda: “Ho visitato lo stabilimento malese per vedere l’installazione dal vivo e poi ho iniziato a parlare con GEW. All’inizio lentamente, poiché sapevamo di aver bisogno di una soluzione complessa e ingegnerizzata con un elevato livello di personalizzazione”. A poco a poco lo slancio è cresciuto mentre lavorava sui requisiti di Panoval con la divisione “Specialist UV” di GEW. Commenta: “Siamo rimasti colpiti dalle persone di GEW… dalla loro reattività e dalla loro capacità di rispondere a tutte le nostre domande, per quanto tecniche. L’importante è lavorare con le persone giuste.”
Van Zwieten ha poi visitato lo stabilimento di produzione di GEW nel Regno Unito durante la costruzione del sistema, offrendo ad entrambe le parti l’opportunità di discutere il sistema in modo più dettagliato e di assicurarsi che fosse sulla buona strada per soddisfare tutti i requisiti e le aspettative. Per quanto riguarda la progettazione, l’installazione e il supporto tecnico continuo del sistema, van Zwieten non ha riserve: “L’intero processo si è svolto senza intoppi, non abbiamo avuto alcun problema. Se si verifica un problema tecnico, disponiamo del monitoraggio remoto di GEW per assisterci, ma abbiamo avuto davvero una buona esperienza con questo sistema. E continua: “Ad oggi, l’unica richiesta che abbiamo avuto per il servizio di monitoraggio remoto sono i report settimanali che riceviamo automaticamente, che ci mostrano informazioni utili per la gestione come tempo di funzionamento, ore di lampada, consumo energetico ed efficienza. Ci dà anche tranquillità perché sappiamo che se dovesse sorgere un problema, verrebbe immediatamente segnalato dalla piattaforma di monitoraggio.”
Come sottolinea van Zwieten, non si è badato a spese nella specifica del nuovo sistema di essiccazione UV, per garantire che soddisfi ogni richiesta per gli anni a venire. Egli commenta: “Un tipico laminatore installerà una o due stazioni lampada e poi sarà soddisfatto. Qui ci siamo differenziati e abbiamo installato una serie di cinque lampade in tandem, il che significa che possiamo modificare la distanza tra l’applicazione chimica e l’indurimento da un lavoro all’altro, consentendoci di soddisfare molti mercati diversi che attualmente non possono essere soddisfatti con questa tecnologia. Per questo abbiamo scelto di collaborare con le persone di GEW, che hanno le competenze tecniche e l’esperienza per un sistema così complesso. Ora attendiamo con impazienza un rapido ritorno sul nostro investimento, con il risparmio energetico e il nuovo lavoro che il sistema UV ci offre.”
I mercati target di Panoval sono l’industria farmaceutica ed elettronica, che richiedono un’etichetta più pulita con proprietà di degassamento residuo inferiori. Van Zwieten spiega: “Il degassamento residuo è il caso in cui un prodotto continua a emettere gas dopo la produzione, e questo può rappresentare un problema serio per i produttori. Nel mondo dell’elettronica, ad esempio, il degassamento può causare guasti elettronici e se si producono articoli costosi come unità ottiche, allora qualsiasi fattore di guasto deve essere ridotto al minimo assoluto, se non può essere eliminato completamente”. E continua: “È qui che il sistema di polimerizzazione UV ci distingue davvero. Abbiamo provato e testato il nostro processo di polimerizzazione nel nostro ambiente di produzione in camera bianca ISO 6 e siamo in grado di produrre laminati con proprietà di degassamento molto, molto inferiori. Ciò ci consente di offrire un prodotto più pulito e di gran lunga superiore a questi produttori specializzati e ai loro trasformatori.”
Con il sistema UV su misura progettato appositamente per Panoval, la distanza tra le teste di rivestimento e le lampade di essiccazione può essere controllata con precisione. Ciò significa che è possibile ottenere l’esposizione ottimale per una moltitudine di applicazioni diverse. Inoltre, il sistema UV è stato progettato con sette alloggiamenti dei gruppi lampada e cinque cassette lampada riposizionabili, il che significa che i gruppi lampada possono essere posizionati in diverse posizioni, per controllare efficacemente il tempo di permanenza. Aumentando il tempo che intercorre tra l’applicazione delle sostanze chimiche al substrato e il punto in cui tali sostanze chimiche vengono polimerizzate, si concede più tempo alla fuoriuscita dei gas indesiderati prima della laminazione. Influisce anche sulla velocità alla quale la macchina può funzionare; il periodo di degassamento più lungo consente di ottenere una polimerizzazione efficace e sicura a velocità di funzionamento fino al 50% più veloci. Come afferma van Zwieten: “Questo ci dà un enorme vantaggio competitivo rispetto a molte aziende statunitensi ed europee, che sono limitate a lavorare a velocità inferiori.”
A dimostrazione della ricerca da parte dell’azienda della soluzione perfetta, Panoval ha anche investito nell’installazione di cinque sensori GEW di monitoraggio UV multipunto (mUVm) su ciascuno dei gruppi lampada UV e collegati al proprio sistema ERP. Questi possono misurare nella posizione centrale della lampada e ai bordi estremi di un nastro da 500 mm e di un nastro da 1050 mm. Oltre alle letture del misuratore di particelle che misurano accuratamente i livelli di degassamento immediatamente dopo la polimerizzazione, mUVm consente al team di produzione di misurare e verificare che sia stato somministrato il livello corretto di dose e intensità UV durante tutto il ciclo di produzione. Con mUVm è possibile generare un certificato di polimerizzazione UV per ogni lotto registrando le uscite UV in tempo reale per ogni lampada. I dati di output UV in tempo reale vengono esportati tramite un’interfaccia API RESTful.
Tuttavia, l’obiettivo di van Zwieten è quello di sviluppare ulteriormente i vantaggi del sistema di monitoraggio UV utilizzando la sua capacità di reporting per ricercare e stabilire livelli di energia ottimali per l’adesività iniziale, l’adesione e il rilascio della gamma principale di prodotti dell’azienda. Le informazioni del sensore UV verranno quindi utilizzate per creare una mappa di polimerizzazione 3D di ogni rotolo jumbo di prodotto, offrendo un elevato livello di tracciabilità ai produttori degli utenti finali. Sebbene questi dati siano particolarmente cruciali per i clienti dei settori farmaceutico, elettronico e aerospaziale, possono anche essere utilizzati per impostare cicli di produzione ripetuti, in modo rapido ed efficiente.
La squadra di Wilco van Zwieten ha dovuto superare anche le difficoltà tecniche create dalle condizioni locali di Ho Chi Minh City. I 18.000 m3/h di aria utilizzata per il raffreddamento vengono aspirati nella camera bianca dall’esterno dell’edificio ad una temperatura ambiente di circa 35°C. Sono stati dotati di filtraggio a due stadi e di circa 25 metri di condotti di ingresso aggiuntivi per ridurre la temperatura dell’aria, l’umidità e qualsiasi particella contaminante all’interno, prima che raggiunga i gruppi lampada.
Il team di produzione è guidato collettivamente da una mentalità pionieristica; il loro obiettivo è utilizzare la ricerca e lo sviluppo per creare prodotti che offrano all’utente finale un vantaggio commerciale. Un esempio di ciò è la produzione di substrati per etichette di pneumatici, utilizzando un raffinato processo di hot melt UV. Come spiega van Zwieten: “Non utilizzeremmo l’hot melt convenzionale per le etichette dei pneumatici perché è piuttosto instabile, soprattutto con grammature più elevate. Ciò fa sì che il convertitore debba ridurre la velocità di conversione poiché le lame di fustellatura si contaminano rapidamente con l’adesivo. Abbiamo invece perfezionato il processo hot melt UV mediante il quale possiamo leggermente sovrapolimerizzare, per creare un adesivo a bassa aderenza con un’adesione finale molto elevata. Ciò significa che il trasformatore può produrre le sue etichette in modo molto più rapido e pulito. È una situazione vantaggiosa per entrambi.”

Sono i vantaggi commerciali a valle che differenziano i loro prodotti UV da quelli convenzionali e più che compensano il costo leggermente più elevato delle materie prime a base UV. In aggiunta a ciò, van Zwieten sottolinea una tendenza del mercato che gioca anche a loro favore: “Sempre più produttori di rivestimenti producono polimeri a base UV e vediamo i prezzi scendere rapidamente… sono già scesi di oltre il 40% negli ultimi tre anni. È solo questione di tempo prima che gli UV prendano il sopravvento.”
Il sistema a cinque lampade di Panoval consente al team di personalizzare il processo di polimerizzazione per ogni singolo lavoro, per ottenere una polimerizzazione insufficiente e eccessiva a piacimento. Come spiega van Zwieten: “Per alcuni lavori è necessario sottocurare e possiamo farlo semplicemente utilizzando una lampada alla fine del percorso. Il vantaggio di questo è che estende il percorso fino a 130 cm, e questo lascia il tempo necessario per il degassamento prima che il rivestimento raggiunga la stazione UV. In questo modo possiamo produrre etichette per applicazioni mediche altamente impegnative, ad esempio, senza rallentare la nostra linea di rivestimento.”
Per quantificare questo aumento di velocità in termini di vantaggio competitivo, van Zwieten continua: “Possiamo eseguire questi particolari lavori fino a 40 metri al minuto, che è molto al di sopra della norma per questo tipo di prodotto specializzato. In Europa e negli Stati Uniti funzionano comunemente a 25 metri al minuto e, di conseguenza, sono significativamente più costosi rispetto a prodotti simili.”
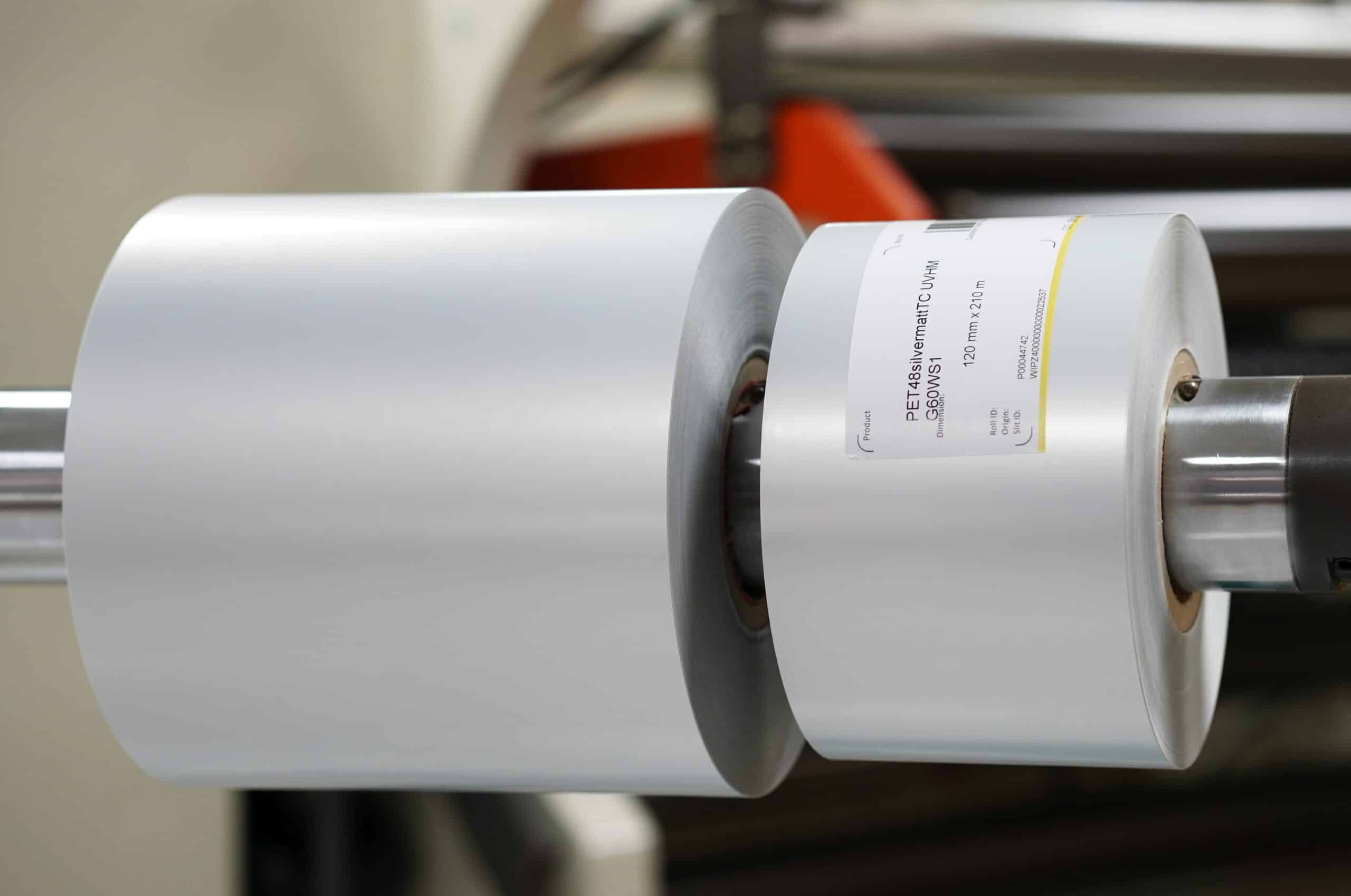
L’etichettatura per applicazioni mediche è spesso richiesta su substrati non tessuti, che assorbono molte più radiazioni rispetto ai poliesteri e ai polipropilene. Ciò significa che anche un’elevata potenza di polimerizzazione UV è un requisito regolare e che la sovrapolimerizzazione può essere facilmente ottenuta con una potenza UV fino a 108 kW a disposizione. La sovrareticolazione UV viene utilizzata per imitare le proprietà più desiderabili degli adesivi a base solvente, per cui il rivestimento viene polimerizzato per diventare a bassa aderenza e asciutto al tatto, ma allo stesso tempo rimane un adesivo altamente coeso che invecchia estremamente bene. Questo processo presenta altri vantaggi, come spiega van Zwieten: “L’adesività iniziale è bassa e consente anche il riposizionamento, ma l’adesione finale è molto forte – supera facilmente i 50 newton – come richiesto per l’etichettatura ad alte prestazioni. E poi torniamo ai vantaggi della conversione, che diventa un processo molto più rapido con le vernici UV cured”. Conclude: “Possiamo ottenere tutti i vantaggi dei rivestimenti a base solvente ma senza il degassamento e gli estraibili, che sono una grande preoccupazione per l’industria medica, aerospaziale ed elettronica.”
Panoval dispone anche di finestre in quarzo GEW “HiC” montate sui gruppi lampada UV, particolarmente adatte alle applicazioni hot melt. Questo speciale tipo di quarzo consente il passaggio di una quantità di energia UVC significativamente maggiore attraverso il rivestimento rispetto al quarzo convenzionale. Come commenta van Zwieten: “Non abbiamo tagliato alcun angolo nelle specifiche del nostro sistema UV e dobbiamo ancora trovare un lavoro che non possa essere svolto. Poiché gestiamo una gamma ampia e diversificata di lavori impegnativi e di breve durata, dovevamo essere sicuri che saremo sempre in grado di raggiungere ciò che vogliamo fare. E se mai dovessimo scoprire di aver bisogno di più potenza, possiamo facilmente aggiungere altre due cassette portalampada negli alloggiamenti liberi.” E aggiunge: “Tuttavia, allo stato attuale, su questa linea possiamo correre a 220 metri al minuto. Stiamo raggiungendo il doppio della velocità di produzione rispetto a un’applicazione equivalente a base solvente. Ad esempio, di recente abbiamo prodotto un’etichetta rimovibile in poliestere con un liner a basso rilascio di silicone a una velocità di 100 metri al minuto con una copertura a basso peso del rivestimento e zero degassamento… e questo, per quanto ne so, è un nuovo record mondiale.”
“Il sistema GEW ha raggiunto esattamente ciò che volevamo. Si sovraindurisce, si sottoindurisce perfettamente. Stiamo risparmiando enormi quantità in termini di consumo di elettricità e riducendo la nostra impronta di carbonio. Se pensate che il nostro vecchio sistema ad acqua richiedeva quasi 40 metri di forni riscaldati a 200 gradi, per far uscire l’acqua… consumavamo circa 1.800 kW l’ora. Nelle vernici all’acqua circa il 40% di ogni chilo è acqua da estrarre. Ora con gli UV possiamo correre a 220 metri al minuto e il massimo che consumiamo è di circa 600kW all’ora. Quindi è un terzo.”
Tuttavia, ci sono altre considerazioni da tenere in considerazione quando si adottano processi di polimerizzazione UV, come sottolinea van Zwieten: “È necessario personale meglio addestrato e dedicato per lavorare e comprendere gli UV, e per cominciare sono necessarie attrezzature migliori. Per fare un confronto, solo in Cina ci sono oltre 1.100 laminatori a base solvente e si tratta di macchine semplici, a basso costo e semplici da utilizzare. Non hai bisogno di un laboratorio. Ma è un gioco pericoloso: è tossico e inquinante e costa molta energia”. Confrontando ciò con i vantaggi degli UV, conclude: “Con gli UV non è necessario un inceneritore, non è tossico, non si corre il rischio di incendio e il risparmio energetico e i benefici ambientali sono davvero impressionanti”. Conclude: “Abbiamo trovato in GEW un partner molto competente e reattivo. A chiunque cerchi una soluzione UV per l’adesivo hot melt, suggerirei di chiamarli.”
Fare clic qui per ulteriori informazioni sul nostro processo UV specializzato.