Questo articolo del Vicepresidente per lo sviluppo aziendale di GEW, Inc., Jennifer Heathcote, illustra come i professionisti possono gestire la quantificazione dell’energia emessa dalle fonti di polimerizzazione UV.
- Comprensione e quantificazione dell'energia emessa dalle fonti di polimerizzazione UV
- Cosa viene misurato e come viene misurato?
- Differenze nell'emissione spettrale per sorgenti di polimerizzazione a mercurio e LED UV
- Come vengono utilizzati nella pratica i grafici dell'emissione spettrale/irradianza?
- Penetrazione della lunghezza d'onda per sistemi di polimerizzazione ad arco con elettrodi e LED UV
- Evoluzione della chimica UV
Comprensione e quantificazione dell’energia emessa dalle fonti di polimerizzazione UV
Nei processi di polimerizzazione UV, l’energia ultravioletta emessa dai vapori di mercurio e dalle lampade LED UV è caratterizzata da irradianza, densità di energia, uscita spettrale e irradianza spettrale. Comprendere questi elementi e il modo in cui vengono quantificati consente agli utenti di abbinare meglio le fonti di polimerizzazione UV alle esigenze di formulazioni, processi e gestione dei materiali. Quando l’emissione UV è opportunamente abbinata, la fotopolimerizzazione efficace ed efficace avviene alle velocità di linea desiderate e alle distanze di lavoro o di offset richieste. Inoltre, quando le finestre operative per l’irraggiamento e la densità energetica vengono mantenute nel tempo, si ottiene un prodotto di qualità costante e ripetibile.
Gli elementi comunemente citati che caratterizzano l’emissione UV includono:
- Irraggiamento (W/cm2) – Si tratta della potenza radiante che arriva a una superficie di polimerizzazione da tutti gli angoli anteriori, per unità di area.1 Viene generalmente riportata come irradianza effettiva su una larghezza di banda definita ed è più significativa se riferita a una distanza di lavoro specifica per il sistema di polimerizzazione UV misurato.
- Densità di energia (J/cm2) – Si tratta dell’energia radiante che arriva alla superficie di polimerizzazione per unità di area.1 Viene generalmente riportata come densità di energia effettiva su una larghezza di banda definita. Anche se può essere considerato come l’irradiazione di picco moltiplicata per il tempo, il calcolo della densità di energia è un po’ più complicato per la maggior parte delle configurazioni di polimerizzazione UV e delle installazioni di linee di produzione. Questo è discusso più avanti nell’articolo.
- Uscita spettrale – Questa è l’emissione radiante (W) di una lampada rispetto alla lunghezza d’onda (nm). Si esprime in W/nm o W/10nm.1
- Irradianza spettrale – Si tratta della potenza radiante di una lampada per unità di area (W/cm2) rispetto alla lunghezza d’onda (nm). In altre parole, è l’irradianza per lunghezza d’onda. Si esprime in W/cm2/nm.
L’irradianza, la densità di energia, l’emissione spettrale e l’irradianza spettrale variano in base al tipo di lampada, al fornitore della lampada, al design del gruppo lampada, all’energia elettrica applicata e alle ore di funzionamento. Inoltre, l’entità dell’irraggiamento e della densità di energia che alla fine raggiungono la superficie di polimerizzazione sono fortemente influenzate dal modo in cui i sistemi sono integrati nelle linee di produzione e dalla cura con cui vengono mantenuti i sistemi dopo la messa in servizio. Fortunatamente, una volta che un sistema di polimerizzazione UV è adeguatamente abbinato a una formulazione e adeguatamente integrato in una linea di produzione, il processo di polimerizzazione è incredibilmente ripetibile e può essere tenuto sotto controllo con la misurazione periodica dell’irraggiamento e della densità di energia insieme alla regolare manutenzione del sistema.
Irradianza
L’irraggiamento (W/cm2) è la potenza di un sistema di polimerizzazione UV in un istante di tempo per unità di area ed è spesso indicato come intensità della lampada. Poiché le unità W/cm2 equivalgono a J/cm2/s, l’irradianza può essere considerata come la velocità con cui la densità di energia (J/cm2) viene erogata alla superficie polimerizzata. In altre parole, l’irradianza è il rateo di dose.
In tutto l’universo, le onde elettromagnetiche di energia divergono l’una dall’altra mentre si allontanano dalla rispettiva fonte di emissione. Poiché le onde divergono con la distanza, diminuisce anche l’entità dell’irradianza corrispondente. Secondo la legge dell’inverso del quadrato, l’irradianza è inversamente proporzionale al quadrato della distanza percorsa. Di conseguenza, se è nota l’irradianza ad una distanza definita da una sorgente emittente, l’irradianza ad una seconda distanza può essere calcolata utilizzando la legge dell’inverso del quadrato.
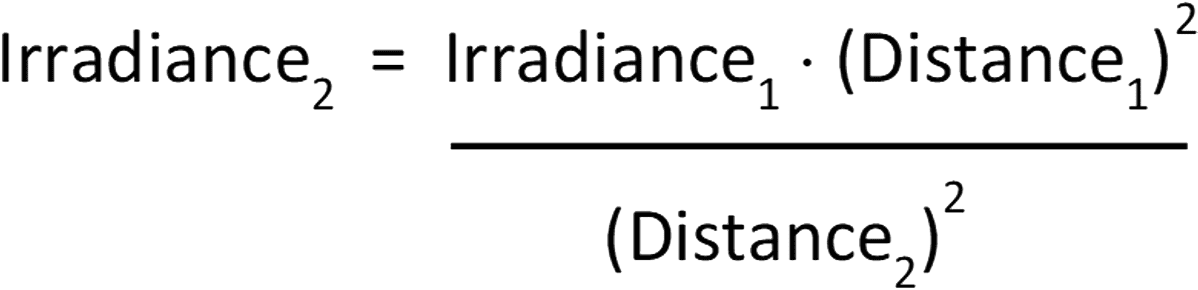
In prossimità delle lampade di polimerizzazione UV, l’irradianza è solo approssimativamente proporzionale alla legge dell’inverso del quadrato. Questo perché gli ingegneri incorporano riflettori e altre ottiche nei progetti dei gruppi lampada per reindirizzare i raggi UV su brevi distanze e ridurre al minimo la diffusione naturale della luce. Inoltre, nel caso dei gruppi lampada UV LED, le sorgenti di emissione sono composte da numerosi minuscoli diodi in cui ciascun diodo funge da sorgente puntiforme separata di luce irradiata. È necessaria una breve distanza affinché le onde emesse da numerose sorgenti puntiformi LED si fondano uniformemente e alla fine formino un’unica sorgente di radiazione uniforme. Riflettori, ottiche e l’uso di più diodi aggirano la legge dell’inverso del quadrato entro brevi distanze dai gruppi lampada per l’essiccazione UV.
Gli ingegneri utilizzano ottiche e riflettori per focalizzare o collimare l’output dei sistemi di polimerizzazione UV. Ottiche e riflettori concentrano i raggi luminosi che successivamente aumentano l’entità dell’irradiazione alla distanza di lavoro prevista o servono a mantenere un’irradianza più costante su un intervallo definito di distanze di lavoro. Per le tradizionali lampade ad arco ad elettrodo e a microonde, l’area di concentrazione focalizzata è nota come punto focale. Al contrario, i sistemi LED convenzionali e UV senza punto focale o altra ottica fanno sì che i raggi luminosi divergano naturalmente l’uno dall’altro non appena escono dal gruppo lampada. Ciò inonda la luce UV su una superficie molto più ampia. Il montaggio di un gruppo lampada in modo tale che la superficie di polimerizzazione sia oltre il punto focale produce un risultato simile. In generale, i sistemi a inondazione, i sistemi montati fuori fuoco e i sistemi montati a distanze di lavoro sempre maggiori determinano una diminuzione dell’irradiazione sulla superficie di polimerizzazione.
Per le lampade ad arco ad elettrodi l’irraggiamento è maggiore nel punto focale. Per i sistemi di polimerizzazione UV LED, che non hanno un punto focale, così come per le lampade convenzionali con profilo Flood, l’irraggiamento è maggiore vicino all’uscita del gruppo lampada o della finestra al quarzo. A causa delle differenze intrinseche nella tecnologia, i sistemi di polimerizzazione LED UV possono essere progettati per emettere valori di irradianza inferiori, simili o sostanzialmente maggiori rispetto alle lampade ai vapori di mercurio a media pressione. I sistemi LED UV, tuttavia, emettono questa irradianza su una banda di lunghezze d’onda molto più ristretta, il che rende difficile il confronto diretto tra i sistemi di polimerizzazione convenzionali e quelli a LED. Come affermato in precedenza, i valori di irradianza per entrambe le tecnologie sono fortemente influenzati dalla distanza percorsa dalla luce. Di conseguenza, la distanza di offset tra un gruppo lampada e la superficie superiore di uno strumento di misurazione UV o tra un gruppo lampada e la superficie di polimerizzazione è significativa e dovrebbe essere sempre annotata durante la configurazione e la tenuta dei registri.
Oltre al fatto che l’irradianza dipende dalle configurazioni del gruppo lampada, come focalizzato o diffuso per le lampade ad arco con elettrodi e collimato o diffuso per i LED UV, l’irradianza emessa da un sistema di essiccazione UV aumenta e diminuisce con i corrispondenti cambiamenti nella potenza della lampada e nella distanza di offset. A condizione che la potenza della lampada e la posizione del gruppo lampada rispetto alla superficie di polimerizzazione non cambino e, ignorando il graduale degrado della lampada nel tempo, l’irradianza rimane costante in ogni punto del profilo di irradianza indipendentemente dalla velocità o dalla lentezza con cui nastri, fogli o parti passano o sostano davanti a un sistema di polimerizzazione UV.
In pratica, poiché la maggior parte dei processi di polimerizzazione UV incorporano qualche forma di movimentazione dei materiali o di automazione del gruppo lampada, la superficie di polimerizzazione generalmente si muove in relazione alla fonte di emissione. Di conseguenza, l’irradianza erogata su una piccola area in movimento sulla superficie di polimerizzazione non è costante nel tempo di esposizione. Questa esposizione dinamica è il risultato di leggere variazioni nell’emissione emessa, fluttuazioni della distanza di lavoro dovute al rimbalzo del nastro o ai profili delle parti sagomate, ritardi nell’attivazione dell’otturatore, una superficie di polimerizzazione che passa davanti a un gruppo lampada fisso o un gruppo lampada che passa davanti a una superficie di polimerizzazione fissa. L’esposizione dinamica si riferisce a qualsiasi processo in cui la superficie polimerizzata subisce un’irradiazione variabile per tutta la durata del tempo di reazione della formulazione.
Immagina una piccola area su una rete, un foglio o una parte molto più grande che si muove verso, sotto e lontano da una fonte di polimerizzazione UV fissa. Quando l’area selezionata si avvicina alla luce, l’irradianza di picco che arriva all’area aumenta rapidamente. L’irradianza nell’area continua ad aumentare fino a raggiungere un valore massimo nel punto in cui l’area passa attraverso il punto focale o il centro del gruppo lampada. Man mano che la stessa piccola area sulla superficie di polimerizzazione si allontana dal punto focale o dal centro del gruppo lampada, l’irradianza di picco che arriva all’area diminuisce rapidamente. I profili di irradianza UV illustrano graficamente come l’irradianza di picco erogata su una superficie polimerizzata varia rispetto al tempo. Per lo scenario appena descritto, il profilo di irradianza UV assomiglia ad una curva a campana.
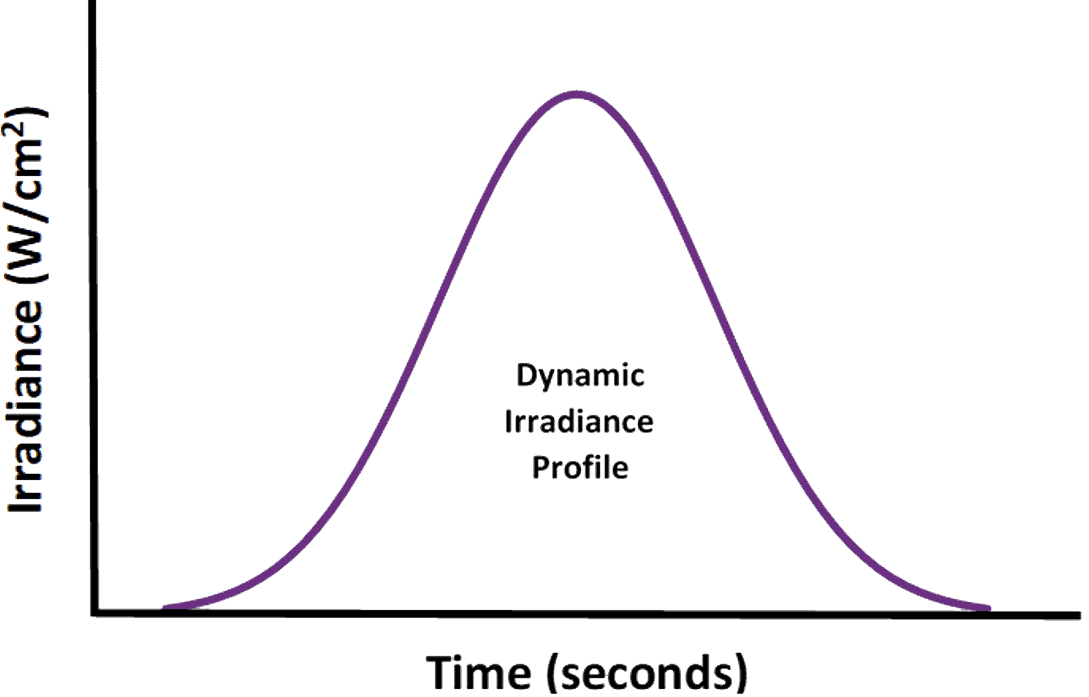
Al contrario, l’esposizione statica si riferisce a qualsiasi processo in cui la superficie polimerizzata subisce un’irradiazione costante per l’intero tempo di reazione della formulazione. Ciò è possibile nelle applicazioni di polimerizzazione spot e area e con camere di polimerizzazione appositamente progettate. In ciascuno di questi casi, il gruppo lampada e la superficie di polimerizzazione non si muovono, l’intera superficie di polimerizzazione è esposta uniformemente durante tutta la reazione e l’energia UV erogata si accende istantaneamente e si spegne istantaneamente. L’esposizione statica è rappresentata dal seguente profilo di irradianza rettangolare.
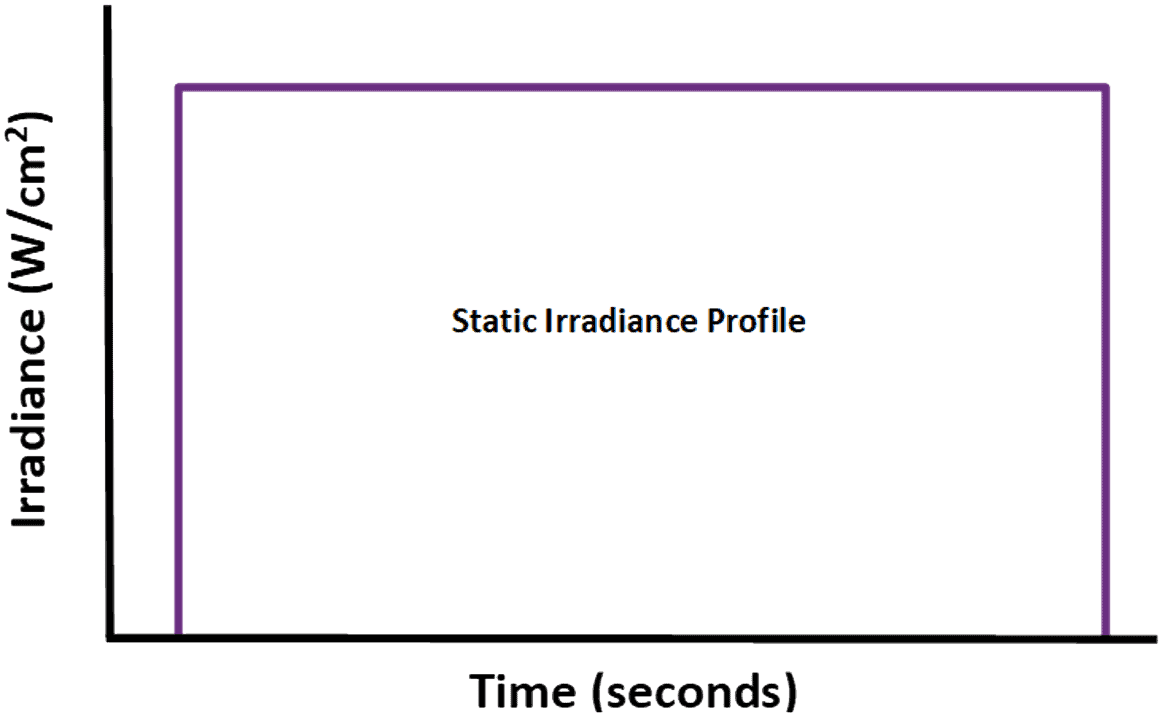
Densità energetica
La densità di energia (J/cm2) è l’energia totale erogata da un sistema nel tempo per unità di area ed è spesso definita dose. Matematicamente, la densità di energia è l’integrale dell’irradianza nel tempo ed è spesso stimata moltiplicando l’irradianza di picco per l’esposizione o il tempo di permanenza. La stima con la moltiplicazione, tuttavia, generalmente produce un valore di densità di energia troppo elevato poiché l’irradiazione sulla superficie di polimerizzazione è raramente statica. Ciò è illustrato con i seguenti profili di irradianza statici e dinamici in cui la densità di energia è equivalente all’area sotto la curva.
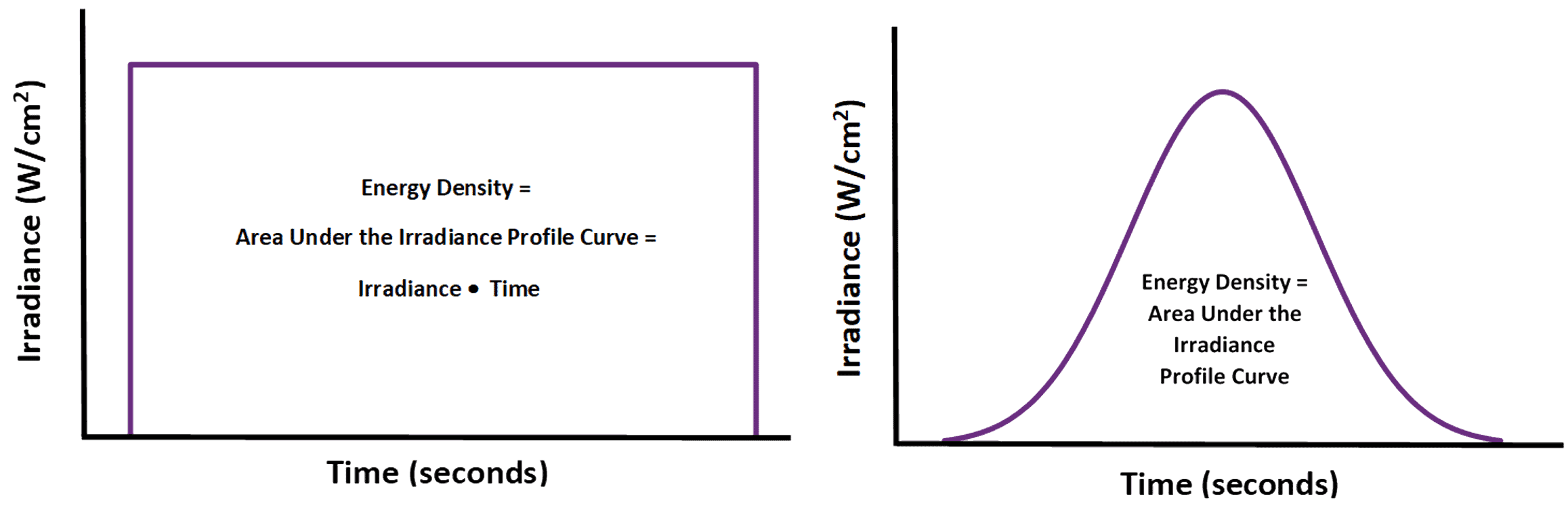
Il profilo rettangolare rappresenta l’esposizione statica in cui l’irradianza è costante nel tempo. Al contrario, il profilo a campana rappresenta l’esposizione dinamica in cui la superficie di polimerizzazione o il gruppo lampada si muovono l’uno rispetto all’altro. L’area sotto il profilo rettangolare può essere facilmente calcolata moltiplicando l’irradianza di picco per il tempo di esposizione totale. Nel caso dell’esposizione dinamica, moltiplicando l’irradianza di picco, che si verifica nella parte superiore della curva a campana, per il tempo di esposizione totale si sovrastima grossolanamente la densità di energia.
La densità energetica può essere aumentata aumentando la potenza della lampada, rallentando la velocità della linea, aumentando il tempo di permanenza, aggiungendo più lampade o facendo passare più volte una superficie di polimerizzazione davanti a una fonte di luce. Sebbene esistano eccezioni relative all’atmosfera, all’integrazione e all’orientamento della lampada, per la maggior parte delle applicazioni la densità energetica è influenzata in misura minima dalla distanza di lavoro. Nel caso dei LED vengono utilizzate anche lampade più larghe con diodi distanziati in modo ottimale per fornire ulteriore densità energetica.
Emissione spettrale e irradianza spettrale
L’emissione spettrale è l’emissione radiante di una lampada (W) rispetto alla lunghezza d’onda (nm). L’emissione spettrale è espressa in W/nm o W/10 nm.1 Strettamente correlato è l’irradianza spettrale, ovvero l’irradianza per unità di lunghezza d’onda (W/cm2/nm).1 Entrambi vengono misurati utilizzando uno spettroradiometro, uno strumento che combina le funzioni di un radiometro e di un monocromatore per misurare l’irradianza in larghezze di banda finemente suddivise.1
Sia la lunghezza d’onda ultravioletta che quella visibile sono generalmente misurate in miliardesimi di metro (0,000000001 m) o nanometri (nm). Per riferimento, un foglio di carta ha uno spessore di circa 100.000 nanometri. L’intervallo spettrale UV standard ISO2 è definito da 10 a 400 nm mentre l’intervallo visibile è da 400 a 700 nm. Ai fini della polimerizzazione UV, gli enti e gli esperti del settore classificano la luce ultravioletta come compresa tra 200 e 450 nm, tra le altre variazioni. Di conseguenza, nella pratica vengono spesso citati e utilizzati intervalli diversi e talvolta sovrapposti. Il modo migliore per illustrare e comunicare la distribuzione della lunghezza d’onda di una fonte di polimerizzazione UV nonché la potenza relativa attraverso la distribuzione è con un grafico di uscita spettrale o di irradianza spettrale.
Un grafico di uscita spettrale/irradianza è un grafico a linee o a barre con l’emissione radiante o l’irradianza di un sistema sull’asse y e le lunghezze d’onda corrispondenti sull’asse x. L’emissione spettrale/irradianza dipende dal tipo di lampada ed è diversa per le lampade a vapori a media pressione al mercurio, ferro e gallio nonché per i LED da 365, 385, 395 e 405 nm. L’emissione spettrale/irradianza dipende anche dalle caratteristiche di progettazione del sistema meccanico ed elettrico che influenzano la direzione in cui la luce viene emessa da un gruppo lampada; proprietà fisiche di riflettori, finestre e altre caratteristiche; la potenza alla quale viene pilotata la lampada; e l’efficacia del sistema di raffreddamento. Il grafico dell’emissione spettrale/irradianza di un prodotto è una specifica fornita dai fornitori di lampade e sistemi. È inteso solo come riferimento e non è qualcosa che viene comunemente misurato o ricreato dagli utenti sul campo della tecnologia. È importante notare che l’emissione spettrale e l’irradianza spettrale delle singole lampade UV o LED differisce significativamente dall’emissione spettrale e dall’irradianza spettrale del sistema di polimerizzazione UV una volta che la sorgente è stata completamente integrata con altri componenti.
L’uscita spettrale/irradianza può essere visualizzata in diversi modi, incluso il valore assoluto espresso in (W/nm) o (W/cm2/nm) o misure arbitrarie, relative e normalizzate (senza unità). I profili normalmente visualizzano le informazioni come grafico a linee o a barre dove i grafici a barre in genere integrano l’output su bande di 10 nm. L’uso di bande da 10 nm rende le informazioni più facili da interpretare e riduce la difficoltà di quantificare gli effetti degli spettri di emissione lineare1. I grafici spettrali relativi e normalizzati sono le rappresentazioni più comuni.
Cosa viene misurato e come viene misurato?
Mentre l’emissione spettrale e l’irradianza spettrale sono specifiche della lampada misurate utilizzando spettroradiometri specializzati, l’irradianza e la densità di energia sono misurabili sul campo utilizzando radiometri portatili meno costosi e disponibili in commercio.
In alcuni casi, come con l’opzione mUVm di GEW, il monitoraggio UV può essere integrato direttamente nel gruppo lampada e nei corrispondenti controlli del sistema. Ogni volta che l’irradianza e la densità di energia vengono misurate con un radiometro, le letture sono sempre relative a una sorgente di calibrazione standard scelta dal fornitore del radiometro. I valori misurati sul campo non sono mai valori assoluti. Si tratta invece di valori relativi che sono direttamente correlati alla fonte di calibrazione di fabbrica. L’implicazione è che misuratori diversi tendono a riportare valori diversi.
Di conseguenza, i radiometri sono utilizzati al meglio come dispositivi di controllo del processo in cui lo stesso misuratore e lo stesso protocollo di misurazione vengono utilizzati in modo coerente per monitorare l’emissione UV nel tempo per un determinato laboratorio o linea di produzione. Quando i valori misurati di irradianza o densità di energia scendono al di sotto dei livelli minimi, è possibile apportare modifiche al sistema per riportare il processo sotto controllo. Va notato che i radiometri sono progettati per misurare lampade a vapori di mercurio o LED. Lo stesso tipo di misuratore non misura entrambe le categorie di sorgenti emittenti.
I radiometri campionano l’irradianza di un sistema numerose volte al secondo su un intervallo specificato di lunghezze d’onda. La frequenza con cui vengono registrati i campioni è nota come frequenza di campionamento. Il campionamento avviene nel tempo man mano che lo strumento passa davanti a una o più sorgenti luminose. L’irradianza di picco del sistema viene segnalata come il singolo valore più grande all’interno dell’insieme di punti dati campionati. I valori separati di irradianza di picco misurati su diverse larghezze di banda come UVC, UVB, UVA e UVV non sono additivi poiché la definizione di irradianza di picco è il massimo valore misurato a una data lunghezza d’onda o su un intervallo di lunghezze d’onda. La gamma di lunghezze d’onda su cui vengono campionati i valori di irradianza è una specifica fissa del misuratore e determinata dalla sensibilità e dalla portata dei fotodiodi del misuratore.
L’insieme completo dei dati relativi all’irradianza di picco raccolti quando un radiometro passa davanti a una sorgente UV costituisce il profilo di irradianza. L’integrazione di quel profilo, che è l’area sotto la curva, è la densità di energia. Per esposizioni dinamiche come il profilo a campana nell’immagine seguente, la densità di energia viene determinata calcolando e sommando numerose aree più piccole. L’area di ogni piccolo rettangolo viene determinata moltiplicando ciascun punto dati sul profilo per il tempo trascorso tra i punti dati. Questo è un metodo ben consolidato per integrare le aree sotto profili non lineari ed è il motivo per cui i radiometri che misurano la densità di energia sono chiamati radiometri integratori.
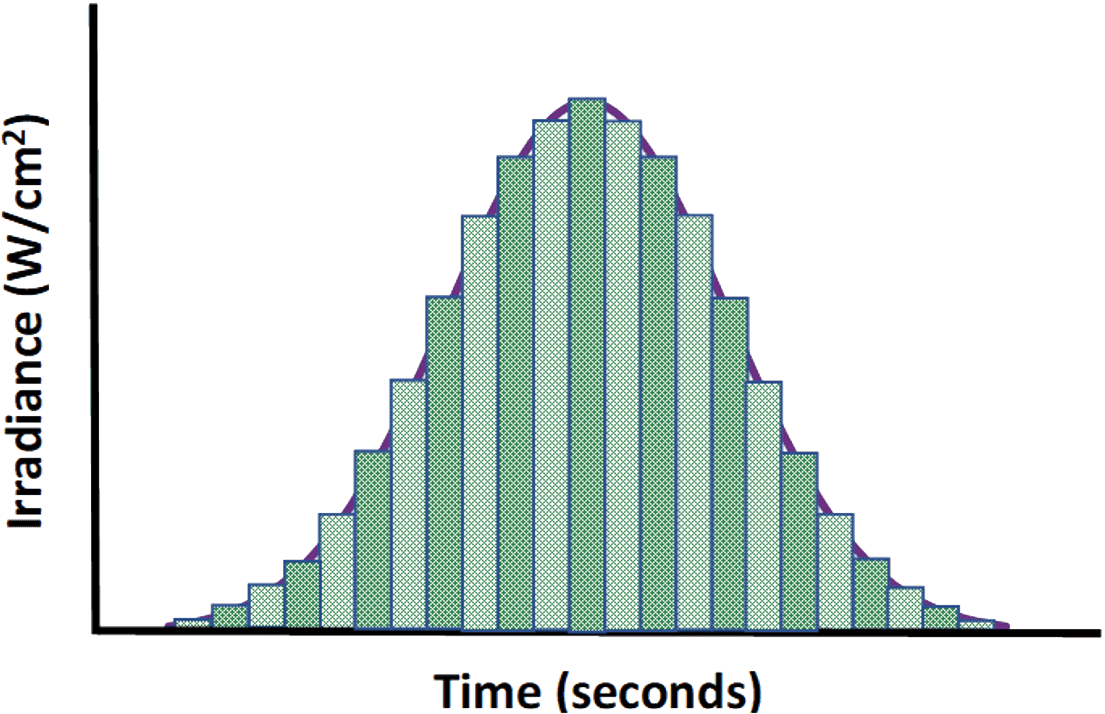
Differenze nell’emissione spettrale per sorgenti di polimerizzazione a mercurio e LED UV
Il rendimento dei sistemi di polimerizzazione UV convenzionali abbraccia le lunghezze d’onda ultraviolette (UV), visibili e infrarosse. Per questo motivo, sia le lampade UV ad arco che quelle a microonde sono considerate a banda larga o ad ampio spettro. L’emissione dei sistemi standard a vapore di mercurio a media pressione copre l’ultravioletto, il visibile e l’infrarosso in proporzioni approssimativamente uguali. La distribuzione spettrale all’interno della banda UV può essere leggermente modificata aggiungendo piccole quantità di droganti metallici come ferro (Fe), gallio (Ga), piombo (Pb), stagno (Sn), bismuto (Bi) o indio (In). Le lampade con metalli aggiunti alla miscela di mercurio di base e gas inerte vengono generalmente chiamate drogate, additive o ad alogenuri metallici.
Al contrario, l’emissione dei LED UV è concentrata all’interno della banda ultravioletta con una certa emissione visibile e nessuna emissione infrarossa. I LED UV emettono luce quando la corrente scorre attraverso una disposizione di diodi a stato solido fabbricati. Numerosi diodi discreti sono assemblati in una singola riga, serie di righe e colonne o in un’altra configurazione. La disposizione dei diodi forma la lunghezza e la larghezza della sorgente di emissione. L’output spettrale dei sistemi LED UV si basa sulla complessa scienza dei materiali in cui centinaia o migliaia di diodi vengono coltivati strato dopo strato su wafer in camere bianche e quindi tagliati a dadini o estratti individualmente dopo la fabbricazione. Le lunghezze d’onda emesse da un LED non sono qualcosa che può essere modificato o regolato successivamente alla produzione; tuttavia, l’entità della sua irradianza è altamente regolabile per un dato sistema di polimerizzazione e generalmente ha una portata maggiore rispetto alle lampade ad arco con elettrodi e a microonde.
Il seguente grafico dell’irradianza spettrale illustra la relazione generale tra una lampada al mercurio a banda larga e i LED UV disponibili in commercio. L’emissione standard di mercuri è rappresentata dai numerosi picchi ombreggiati in verde mentre l’emissione di LED UV è rappresentata dalle curve a campana viola più alte. Circa un terzo della produzione di mercurio rientra nella regione degli infrarossi (da 700 nm a 1 mm) situata a destra della banda visibile e non mostrata nell’illustrazione. Al contrario, i sistemi LED UV sono privi di infrarossi, il che significa che trasferiscono molto meno calore totale alla superficie di polimerizzazione rispetto alle tradizionali lampade al mercurio. Le lunghezze d’onda ultraviolette, tuttavia, sono ancora una forma di energia irradiata e una parte dell’energia UV viene infine convertita in calore termico quando raggiunge una superficie.
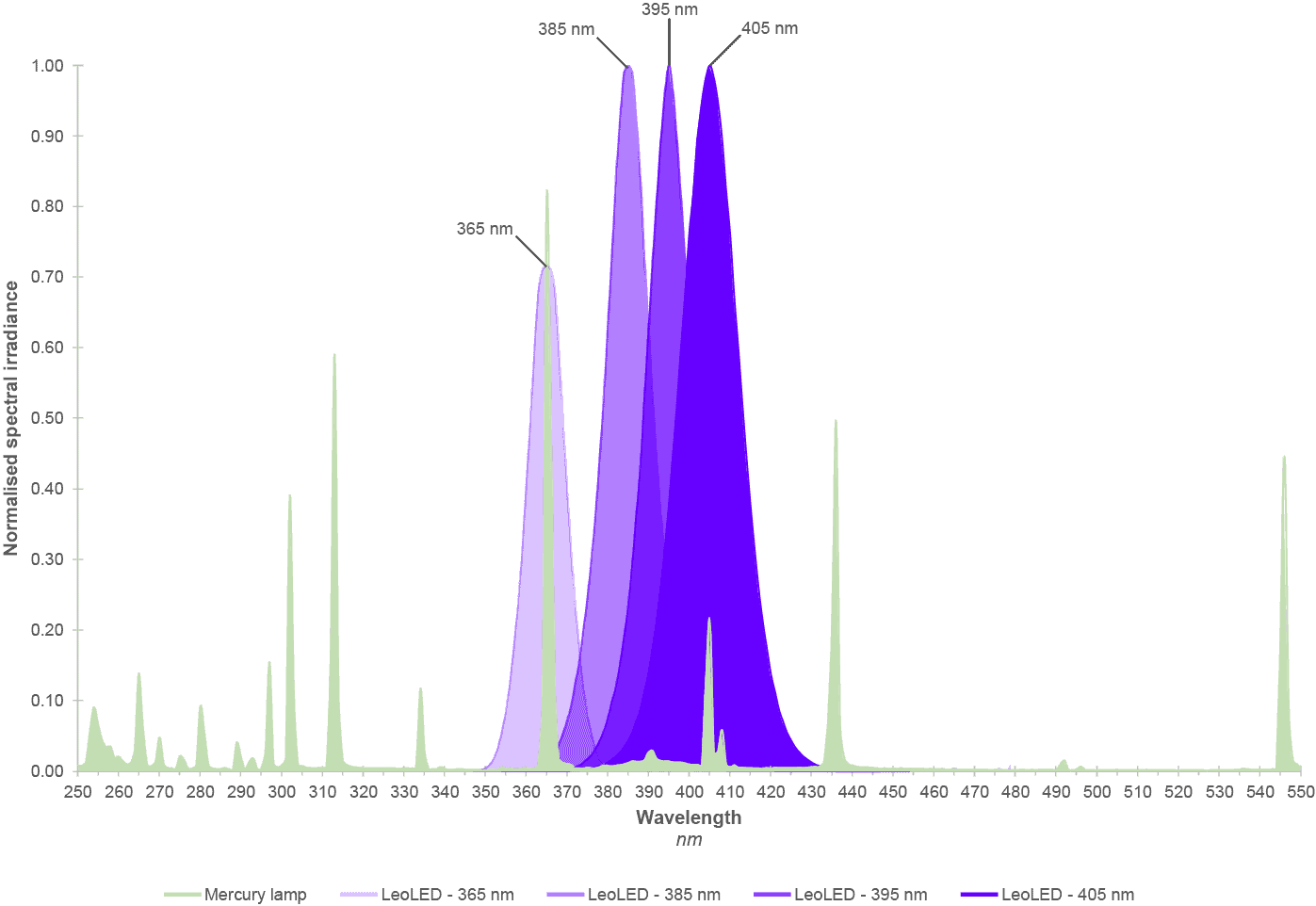
Quali informazioni importanti comunica questo grafico dell’irradianza spettrale?
Il grafico dell’irradianza spettrale illustra chiaramente la differenza tra l’emissione di mercurio (Hg) a banda larga e l’emissione quasi monocromatica della tecnologia LED UV attraverso le lunghezze d’onda UVC (da 200 a 285 nm), UVB (da 285 a 315 nm), UVA (da 315 a 400 nm), UVV (da 400 a 450 nm) e visibile (da 400 a 700 nm). In secondo luogo, dimostra come l’entità relativa dell’irradiamento varia in base alla lunghezza d’onda per le lampade a banda larga e il fatto che sono possibili irradiazioni maggiori con i LED UV che con il mercurio. Infine, sebbene sia le lampade al mercurio che i sistemi LED UV emettano energia UV, chiaramente esistono differenze significative nella lunghezza d’onda e nell’irradianza che devono essere prese in considerazione nello sviluppo del sistema, della formulazione e dell’applicazione.
Va sottolineato che questa tabella è un’illustrazione generale di una tipica lampada ad arco ad elettrodi GEW e dei sistemi LED GEW disponibili in commercio. La distribuzione della lampada ad arco sarebbe leggermente diversa per un altro prodotto e significativamente diversa per una lampada additiva. Dal punto di vista dell’approvvigionamento, i LED UV vengono forniti e prezzati dai produttori di semiconduttori in base alla tolleranza della lunghezza d’onda e all’output con una tolleranza tipica di ±5 nm. Di conseguenza, c’è sempre qualche leggera deviazione nell’accumulo dei diodi che influisce sul profilo spettrale e sulla lunghezza d’onda al quale le curve LED raggiungono il picco. Per quanto riguarda i LED, piccoli spostamenti della lunghezza d’onda generalmente non producono una grande differenza nella polimerizzazione. Per la maggior parte delle applicazioni di polimerizzazione dei LED UV, è l’entità dell’irradiazione e la corrispondente densità di energia a una determinata lunghezza d’onda dei LED UV che svolgono un ruolo maggiore nella reticolazione.
Come vengono utilizzati nella pratica i grafici dell’emissione spettrale/irradianza?
I grafici di emissione spettrale/irradianza sono uno strumento utilizzato principalmente per confrontare diverse lampade di polimerizzazione o progetti di sistemi e abbinarli correttamente ai pacchetti di fotoiniziatori e al caricamento di pigmenti delle formulazioni UV esistenti. Anche i formulatori e i fornitori di materie prime si affidano ai grafici di emissione spettrale/irradianza per sviluppare nuovi prodotti chimici. Non tutte le sorgenti UV trattano tutte le formulazioni e alcune emissioni spettrali sono più adatte ad alcune applicazioni rispetto ad altre. Questo perché i formulatori scelgono da una gamma di fotoiniziatori disponibili in commercio. Il fotoiniziatore è la parte della chimica che assorbe la luce UV e determina la reticolazione all’interno del polimero. Anche se i fotoiniziatori assorbono la luce UV su un ampio intervallo di lunghezze d’onda, un dato fotoiniziatore è sempre più reattivo a determinate lunghezze d’onda e richiede una soglia minima di irradiamento per avviarsi. Diversi fotoiniziatori producono anche diverse proprietà polimeriche estetiche e funzionali a seconda del loro design, della loro reazione con l’energia UV e della loro reazione con il resto della chimica. I formulatori valutano le curve di assorbimento dei fotoiniziatori disponibili rispetto ai grafici di output spettrali e prendono decisioni di compromesso e miscelazione in base alle esigenze delle linee di produzione e delle presse, nonché ai requisiti di utilizzo del prodotto finale.
Penetrazione della lunghezza d’onda per sistemi di polimerizzazione ad arco con elettrodi e LED UV
Come illustra l’immagine seguente, le lunghezze d’onda UVA e UVV più lunghe penetrano in profondità negli inchiostri, nei rivestimenti e negli adesivi mentre le lunghezze d’onda UVC più corte vengono assorbite sulla superficie dei prodotti chimici. Sulla base di queste informazioni, nonché dell’emissione spettrale e dell’irradiazione spettrale delle unità di polimerizzazione commerciali, i formulatori raccomandano quali sorgenti e tipi di lampade sono più adatti ai loro inchiostri, rivestimenti e adesivi. Queste raccomandazioni si presentano sotto forma di specifiche della lampada (mercurio, ferro, gallio, ecc.) o preferenze di lunghezza d’onda del LED (365, 385, 395 o 405 nm). In definitiva, i formulatori hanno il compito di assicurarsi che i loro prodotti funzionino con un’ampia gamma di sistemi di polimerizzazione UV che non necessariamente emettono lo stesso risultato, il che non è sempre un compito facile.
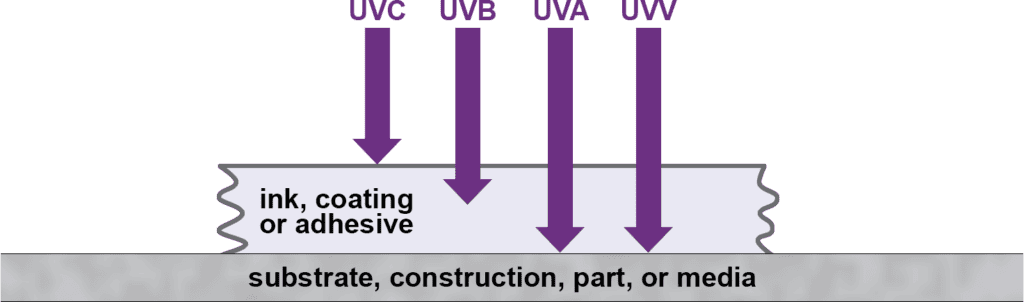
Non esiste una sorgente LED UV che imiti direttamente una lampada al mercurio ad ampio spettro, ma lunghezze d’onda più lunghe emesse dai LED fanno sì che la distribuzione spettrale sia più simile alla parte superiore di una lampada al ferro o al gallio che emette anche una certa uscita nell’intervallo compreso tra 385 e 405 nm. I LED a 385, 395 e 405 nm, nonché le lampade drogate con ferro e gallio, utilizzano tutti lunghezze d’onda più lunghe, quasi visibili, per penetrare in profondità nella chimica e produrre una migliore polimerizzazione, in particolare con formulazioni più spesse, bianche opache e altamente pigmentate. Per i rivestimenti trasparenti UV LED, la sfida principale è stata ottenere una polimerizzazione superficiale dura, resistente agli agenti chimici e ai graffi senza ingiallimento. Questo perché la maggior parte delle formulazioni di rivestimento si basano su lunghezze d’onda UVC più corte emesse da lampade a banda larga per la reticolazione in superficie, e i fotoiniziatori che reagiscono a lunghezze d’onda UV-LED più lunghe possono ingiallire o appannarsi durante l’esposizione. Sebbene questo leggero scolorimento possa essere facilmente mascherato con i pigmenti dell’inchiostro, può essere più evidente con la chimica trasparente.
In generale, i sistemi LED UV presentano un vantaggio rispetto ai sistemi convenzionali in termini di polimerizzazione più profonda. Ciò è dovuto alla concentrazione delle lunghezze d’onda UVA e UVV; tuttavia, i LED UV possono avere difficoltà con la polimerizzazione superficiale quando le formulazioni non sono ottimizzate per l’emissione di fonti che non emettono UVC. Se non adeguatamente abbinata, la polimerizzazione LED UV può lasciare alcune formulazioni appiccicose o unte al tatto. L’ottimizzazione della chimica, la corretta selezione di una sorgente LED UV, l’utilizzo di un’irradiazione più elevata e un’integrazione ponderata possono spesso eliminare i problemi di polimerizzazione superficiale. L’aggiunta di diodi UVC a un dispositivo di polimerizzazione a LED potrebbe in definitiva rivelarsi necessaria per rivestimenti industriali più impegnativi; tuttavia, nonostante il fatto che i LED UVC tra 275 e 285 nm abbiano apportato miglioramenti significativi in termini di irradianza di picco, affidabilità e durata, la tecnologia è indietro rispetto a quella dei LED UVA e non è ancora economicamente sostenibile per la maggior parte delle applicazioni. La maggior parte dei sistemi di polimerizzazione LED UV installati e operativi oggi sulle linee di produzione sono a 395 nm e la maggior parte degli inchiostri, rivestimenti e adesivi utilizzati nelle applicazioni di stampa grafica sono progettati per polimerizzare a questa lunghezza d’onda.
Irradianza, densità di energia e lunghezza d’onda
L’irraggiamento, la densità di energia e la lunghezza d’onda svolgono tutti un ruolo fondamentale nella polimerizzazione UV. Innanzitutto, è necessario fornire alla superficie di indurimento un livello minimo di irradiazione a lunghezze d’onda facilmente assorbibili dal pacchetto fotoiniziatore. In queste condizioni, i fotoiniziatori assorbono l’energia ultravioletta, generano radicali liberi e determinano la reticolazione all’interno della chimica. Nei processi di polimerizzazione UV dinamici, le code più esterne di un profilo di irradianza a campana spesso scendono al di sotto della soglia minima di irradianza e non producono abbastanza reticolazione all’interno della chimica, ma quando la superficie di polimerizzazione si avvicina al gruppo lampada, si stabilisce rapidamente un’irradianza più adatta. In secondo luogo, la soglia minima di irradianza o superiore deve essere mantenuta per tutta la durata della reazione. Infine, una volta erogata e mantenuta l’irradianza necessaria sulla superficie di polimerizzazione, la densità di energia diventa il fattore determinante per la polimerizzazione e il fattore limitante per la massima velocità di linea possibile o il tempo di ciclo più breve possibile. In altre parole, la densità di energia contribuisce in modo significativo alla velocità massima di movimentazione dei materiali di una linea di produzione e al grado di fotopolimerizzazione ottenibile negli inchiostri UV, nei rivestimenti e negli adesivi.
Evoluzione della chimica UV
Per quasi 70 anni, a seconda del mercato e dell’applicazione, l’industria della polimerizzazione UV ha formulato sostanze chimiche per le emissioni spettrali del mercurio convenzionale e delle lampade drogate con mercurio. Tutta la chimica storica utilizza materie prime appositamente progettate per rispondere all’emissione ad ampio spettro del mercurio. Il lavoro di sviluppo dedicato nella chimica dei LED UVA a banda stretta tra alcuni formulatori è iniziato tra il 2005 e il 2010. La maggior parte del settore della polimerizzazione consolidata, tuttavia, ha ritardato il coinvolgimento fino a quando gli utenti finali non sono diventati più interessati e la fattibilità e l’economia della polimerizzazione UV LED non sono migliorate. Altri formulatori sono entrati tra il 2010 e il 2020, e molti altri, in particolare nel settore dei rivestimenti industriali, stanno iniziando proprio adesso mentre il calendario si avvicina al 2021. Lo stesso si può dire di molti fornitori di sistemi di polimerizzazione convenzionali che hanno ritardato il rilascio di sistemi LED UV fino al materializzarsi della domanda del mercato.
In generale, la chimica UV convenzionalmente formulata progettata per sistemi di lampade al mercurio ad ampio spettro non polimerizza bene con lunghezze d’onda più lunghe e LED UV quasi monocromatici. A causa delle differenze nell’emissione spettrale, la chimica convenzionale deve essere riformulata per polimerizzare completamente con una sorgente LED UV. Man mano che sempre più aziende produttrici di inchiostri, rivestimenti e adesivi sviluppano offerte di LED UV, progettano sempre più prodotti chimici in modo tale che una singola formulazione possa essere polimerizzata con il LED pur essendo retrocompatibile con le lampade a banda larga convenzionali. Questa è nota come chimica a doppia polimerizzazione e ha lo scopo di contribuire a ridurre gli SKU e facilitare la transizione alla tecnologia LED UV.
Nei prossimi anni, sempre più formulazioni avranno capacità di doppia polimerizzazione e le formulazioni contenenti solo mercurio saranno rese ridondanti e alla fine interrotte. Ciò non significa che tutto ciò che è stato storicamente progettato per le lampade ad arco a elettrodi scomparirà domani poiché molti settori, in particolare quelli che utilizzano inchiostri e rivestimenti industriali altamente funzionali, nonché quelli che eseguono complicati profili di parti 3D e polimerizzano su distanze di lavoro maggiori, richiedono ulteriore lavoro di sviluppo su formulazioni, lampade e integrazione. Questa affermazione significa semplicemente che è necessario prestare attenzione a ciò che sta accadendo in ogni specifico settore per comprendere l’impatto dei LED sui processi di produzione UV esistenti. È in atto il passaggio all’UV LED; tuttavia, è calcolato e graduale rispetto alle esigenze di ciascun settore e applicazione. Prestare attenzione all’output spettrale, all’irradianza spettrale, all’irradianza e alle esigenze di densità energetica di un’applicazione è fondamentale per determinare se una specifica lampada ad arco con elettrodi o uno specifico sistema di polimerizzazione a LED UV polimerizzerà un inchiostro, un rivestimento o un adesivo e quale tipo di lampada o lunghezza d’onda del LED è ottimale per il processo e la chimica complessivi.
1RadTech North America. (2005). Glossary of Terms – Terminology Used for Ultraviolet (UV) Curing Process Design and Measurement. RadTech UV Measurements Group. pp. 1 – 6. https://www.radtech.org/images/pdf_upload/UVGLOSS_rev4-05.pdf 2International Organization for Standardization.