A proposito di Coleus
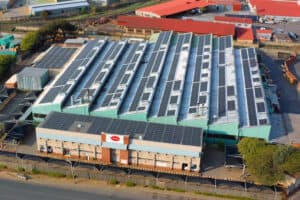
Coleus Packaging è il fornitore più grande e dominante di chiusure metalliche per bottiglie, note come corone, per le industrie della birra e dell’imbottigliamento nell’Africa meridionale. L’azienda produce oltre sette miliardi di corone all’anno, rifornendo più di 10 paesi. Questo immenso volume è ottenuto attraverso l’uso di tecnologie avanzate e materie prime di alto livello, concentrandosi al contempo sulla creazione di soluzioni di imballaggio in metallo con l’impronta ecologica più bassa possibile.
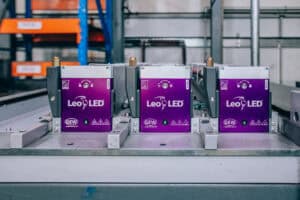
Ian Victor, amministratore delegato di Coleus, presenta l’azienda: “Coleus in realtà risale probabilmente a circa 30 o 40 anni fa, i clienti tipici sono le aziende produttrici di birra come AB InBev, Heineken, Distell… e poi ci sono i birrifici più piccoli. Coleus è l’unico fornitore di corone in metallo e rifornisce tutti i diversi birrifici della regione della Comunità per lo sviluppo dell’Africa meridionale (SADC). Ho assunto la carica di MD nel 2022, sono un ingegnere di professione, quindi guardiamo sempre ai cambiamenti tecnologici e ovviamente alle efficienze che ne derivano.
La vita prima dei LED UV

Victor ricorda un momento in cui Coleus utilizzava la convenzionale polimerizzazione ad arco UV nello stabilimento, prima del passaggio alla tecnologia UV LED sulla sua macchina da stampa Crabtree Fastready, nel giugno 2024: “Ricordo abbastanza chiaramente quando sono arrivato qui per la prima volta e ho visto il modo in cui effettivamente polimerizzano con il mercurio, con questi enormi e grandi trasformatori e alimentatori. Abbiamo deciso di provare a ridurre il consumo energetico e ho motivato il progetto sulla base del cambiamento tecnologico. La tecnologia dovrebbe essere in grado di darti una migliore efficienza, un minor consumo di energia e così via”.
Alla scoperta di GEW e SArepco

E continua: “Nelle fasi iniziali avevamo la possibilità di passare al mercurio UV o di passare all’aggiornamento al sistema LED, e in realtà siamo andati a Crabtree, ed è lì che è venuto fuori il nome GEW. Abbiamo poi scoperto che gli agenti locali di SArepco avevano una grande conoscenza: penso che la decisione che abbiamo preso di utilizzare SArepco sia stata la decisione migliore, perché è stata un’installazione fenomenale, molto ben fatta e molto professionale.”
Dopo aver preso la decisione di passare ai LED UV, il team Coleus ha lavorato a stretto contatto con gli ingegneri progettisti di GEW per garantire la configurazione ottimale per la propria macchina. Hennie Fourie, Senior Printer presso Coleus, descrive la loro configurazione: “Abbiamo installato il sistema a sei lampade LED, quindi c’è una lampada dopo l’unità uno, due e poi tre, e poi abbiamo tre lampade dopo l’unità quattro per la polimerizzazione finale.”
Le differenze apportate dai LED UV

Fourie spiega i miglioramenti che il team ha riscontrato da quando ha abbandonato l’arco UV: “Bene, il sistema di essiccazione è molto importante per la qualità della stampa, non vogliamo controspinta o problemi di qualità. Quindi, se hai iniziato il lavoro, significa che la stampa si stacca dal lato di stampa verso l’interno della corona. Con il mercurio, abbiamo avuto problemi con la compensazione sul bianco e nero dove non si polimerizzava correttamente, quindi ci dava problemi di qualità… e se guardi i vecchi sistemi convenzionali, dove hai un grande forno, ci sono molti cambiamenti di colore, graffi, anche lì qualsiasi cosa può andare storta. Ora, con il sistema LED, abbiamo molti meno problemi legati alla stampa… problemi di asciugatura e polimerizzazione.”
Rennie De Preez è Operations Executive nell’area Produzione e Ingegneria di Coleus. Commenta i vantaggi riscontrati con il LED UV, in particolare per quanto riguarda la riduzione degli sprechi, la produttività e il risparmio energetico: “Il LED UV ha migliorato enormemente la qualità dei nostri prodotti. In termini di scarti, abbiamo registrato una media di circa il 2% solo sulla qualità di stampa per bloccaggio e controstampa, ma adesso con il nuovo sistema LED siamo scesi allo 0,1%. In termini di produzione, quando eravamo sotto i raggi UV, lavoravamo a 3.500 fogli all’ora, ma ora arriviamo a 4.500 fogli… è un enorme miglioramento.”
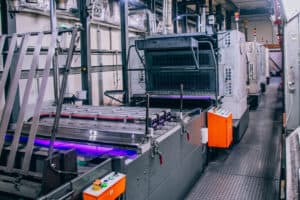
Conclude: “Non c’è una seconda possibilità per i lavori. Ogni lavoro, una volta passato alla macchina da stampa, arriva direttamente al cliente. Abbiamo effettuato alcune registrazioni sul risparmio sui costi elettrici, in realtà siamo seduti su un risparmio del 62% rispetto al sistema UV e al LED.
Victor è d’accordo e sottolinea come il risparmio energetico e l’efficienza del sistema dei LED UV siano ulteriormente migliorati: “Abbiamo fatto la valutazione tecnica, abbiamo notato che il consumo del sistema LED era molto inferiore a quello del mercurio UV. Anche il guadagno in termini di efficienza era abbastanza evidente, perché con il sistema UV al mercurio c’è un intero periodo di riscaldamento prima di poterlo effettivamente utilizzare, mentre con il sistema LED lo accendi e lo usi immediatamente.”

Il fatto che questa significativa riduzione dell’impronta di carbonio possa essere chiaramente dimostrata ai clienti dà a Coleus un vantaggio competitivo significativo, come spiega Victor: “Se, su base annuale, fossimo in grado di mostrare a grandi aziende come AB InBev e Heineken che stiamo riducendo il consumo di energia, ciò ovviamente influenzerebbe la loro decisione di stipulare accordi con noi. L’utilizzo delle credenziali ambientali è estremamente importante, fa effettivamente parte del processo di gara. C’è un vantaggio socio-economico, c’è un vantaggio per i clienti, c’è un vantaggio in termini di impatto ambientale ed è sicuramente un grande strumento di vendita per attirare nuovi clienti”.
Installazione
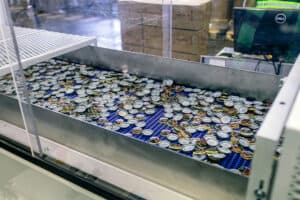
Il team Coleus desiderava un’interruzione minima del programma di produzione durante l’installazione e questo è stato ottenuto, come spiega De Preez: “Quando abbiamo eseguito l’installazione sul LED, tutto è andato liscio, senza problemi. Il team GEW mi ha chiesto un’installazione di nove giorni e l’hanno fatta in sei giorni.” Commenta anche i requisiti di spazio della nuova tecnologia: “Quando si tratta di progettazione, con il sistema precedente dovevo riempire due pareti, dove devo impilare tutte queste apparecchiature elettriche e di raffreddamento e ora con il sistema LED ci sono solo due unità sedute lì e che gestiscono l’intero posto. Lo consiglio vivamente!”
De Preez conclude sull’argomento: “Adesso con il LED, i ragazzi lo fanno con il sorriso. C’è meno trasferimento di calore dal LED ai fogli e ciò migliora anche l’impilamento. Ora con l’unità LED… impilamento perfetto.”
Il passaggio agli inchiostri UV LED

Tanto per cominciare, Coleus aveva alcuni ostacoli da superare quando si trattava di lavorare con gli inchiostri UV LED, come spiega Fourie: “In Sud Africa, l’inchiostro LED non è disponibile gratuitamente, quindi con l’aiuto di un fornitore di inchiostri abbiamo allestito una cucina per gli inchiostri e abbiamo iniziato a mescolare i nostri inchiostri. All’inizio è stato difficile a causa della differenza di densità e pigmento, ma col passare del tempo abbiamo imparato a rispettare lo standard di colore precedente, al 100%”.
Dopo aver superato questi problemi precedenti, Fourie e il suo team hanno scoperto alcuni vantaggi significativi: “Su alcuni lavori in cui stampavamo il doppio bianco, possiamo farla franca con un bianco e anche il nero risulta più denso e di migliore qualità, quindi usi meno inchiostro e ottieni una stampa di qualità molto migliore. L’inchiostro LED è più costoso per chilogrammo, ma ci sono alcuni lavori in cui utilizziamo fino al 50% in meno sullo stesso colore… sì, il 50% in meno – quindi alla fine, penso che siamo più o meno in pareggio – e poi anche le lampade, nel precedente sistema al mercurio avevamo sette lampade, dovevamo sostituirle ogni 1.000 ore. Ora con il sistema LED abbiamo sei lampade e dobbiamo sostituirle solo ogni 40.000 ore”.
Migliorare l’ambiente di lavoro e la produttività
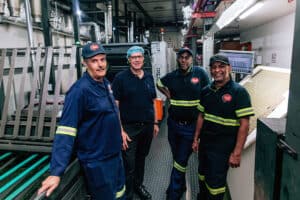
Victor rivolge l’attenzione al miglioramento positivo delle condizioni di lavoro: “Abbiamo effettivamente creato un ambiente di lavoro molto migliore per i nostri dipendenti perché l’area in cui si trova la stampante è diventata estremamente calda con il sistema UV al mercurio. Ora con il LED hai ridotto la temperatura, quindi l’ambiente di lavoro per i lavoratori è migliore.” Poi passa alla questione fondamentale della produttività dell’impianto: “È tutta una questione di efficienza, più corone riesci a ricavare più puoi vendere. Quando ho iniziato qui probabilmente guadagnavamo circa 6 miliardi di corone… siamo oltre 7 miliardi di corone, quindi abbiamo già avuto un miglioramento di quasi il 20%.”
Affidabilità e conclusioni
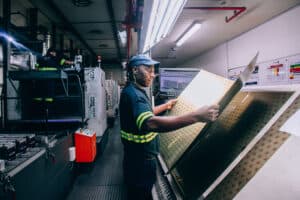
Hennie Fourie riassume il suo pensiero sulla nuova tecnologia: “Sì, il sistema LED mi ha risparmiato un sacco di mal di testa. Nel sistema precedente ero responsabile di risolvere tutti gli errori dell’otturatore, e ce n’erano molti, quindi ci sono molti, molti meno problemi per me.”
Rennie De Preez è chiaro nella sua valutazione: “Mi ha davvero cambiato la vita. In confronto al vecchio sistema, c’erano molti tempi di inattività, c’erano molte chiamate… i ragazzi mi svegliavano di notte. Ora con il nuovo sistema LED non ho più notti insonni! Per quanto riguarda gli operatori, il mio team che lavora con questa unità, il sistema è come per magia, sanno che ogni volta che avviano la macchina da stampa, la stampante funziona, l’unità è lì… questo è quello che vogliono, un’attrezzatura affidabile che renda il loro lavoro, la loro vita, il loro ambiente di lavoro molto più felici.”
Ian Victor conclude con un punto di vista ponderato e qualche consiglio prudente: “Penso che la gente pensi che in Africa siamo sempre indietro rispetto ai tempi, ma non è così. Qui siamo sulla punta dell’Africa, lontano da tutti i grandi OEM… dall’Europa, dove tutti guardano con ammirazione… e noi siamo effettivamente in testa al gruppo.
“Chiunque intenda convertirsi al LED capirà i vantaggi molto, molto rapidamente. Ottieni il supporto giusto, contatta le persone giuste, parla con gli OEM, fai i compiti, parla con i ragazzi dell’inchiostro, assicurati che supportino il sistema che stai installando. È la strada da percorrere, è il futuro, e più velocemente lo fai, meglio è.
Guarda subito il video del caso di studio Coleus
Per saperne di più su LeoLED2, il sistema di polimerizzazione LED UV ad alta potenza di GEW per applicazioni di decorazione dei metalli, vai qui.
Un ringraziamento a Coleus e al nostro distributore in Sud Africa, SArepco, che hanno completato l’installazione.